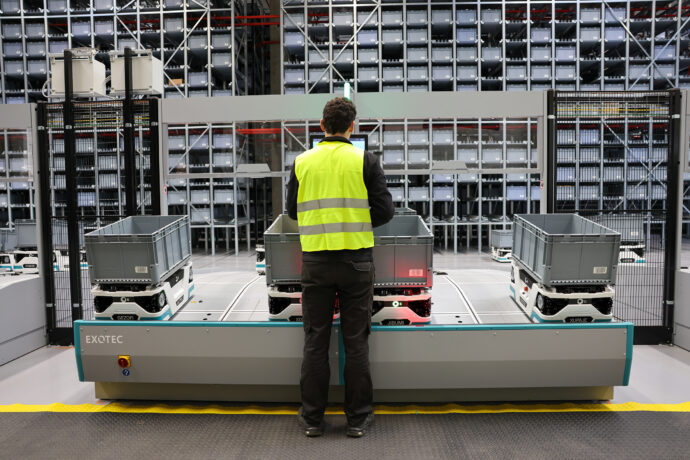
Accelerated Throughput
Pick from up to 600 containers per hour at each station
The Exotec® Skypod® system is an Automated Storage and Retrieval System (AS/RS) that simplifies warehouse processes by reducing the need for extra equipment, saving space, time, and costs
Achieve the optimal mix of AS/RS performance and flexibility to stay ahead in the fast-changing world of logistics
Pick from up to 600 containers per hour at each station
Access any SKU in the system within two minutes
Utilize vertical space with racks reaching up to 45 feet (14 meters)
Reduce fulfillment steps to minimize order touches and improve accuracy
Smart software seamlessly adjusts to dynamic order volumes
Gain peace of mind with a trusted AS/RS partner
Exotec is redefining AS/RS by eliminating complexity and pushing the boundaries of efficiency, flexibility, and performance. Our innovative approach delivers a smarter, more agile solution for modern warehouses.
Ready to transform your warehouse operations? Contact us today to learn more about Skypod system.