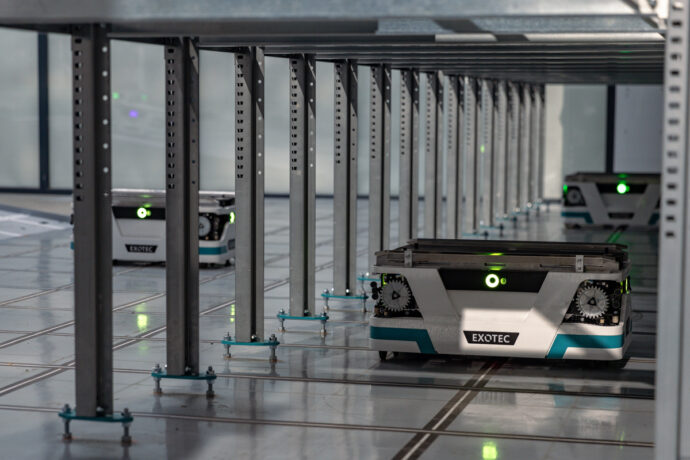
신속한 대응
변화하는 수요와 운영 요구사항에 더 빠르게 대응하세요.
Exotec의 창고 자동화 솔루션은 고객의 비즈니스 요구에 맞게 맞춤화할 수 있습니다. 확장성과 적응성이 뛰어나 비즈니스 성장에 따라 확장할 수 있습니다. 또한 Deepsky®(소프트웨어)를 통해 실시간 재고 데이터와 귀중한 운영 인사이트에 액세스하여 항상 한발 앞서가는 운영을 할 수 있습니다.
변화하는 수요와 운영 요구사항에 더 빠르게 대응하세요.
창고 공간을 최적으로 활용할 수 있도록 밀도를 높입니다
재고 관리 및 주문 이행의 정확성을 향상하세요
재고 관리 및 주문 이행의 정확성을 향상하세요.
성수기 및 계절별 제품을 원활하게 처리할 수 있는 유연성을 누리세요.
엑소텍이 계약상 보장하는 성능을 신뢰하세요.
종합적인 AS/RS 창고 솔루션으로 Exotec®의 차별성을 발견하세요. Skypod® 시스템은 AMR, 피킹 스테이션, 컨베이어 시스템, 첨단 Deepsky® WES를 원활하게 통합합니다. 이러한 총체적인 접근 방식은 유지보수 서비스 및 연중무휴 24시간 관제 센터 지원과 결합하여 안정적인 창고 관리를 보장하고 실시간 인사이트를 제공하여 전체 운영을 쉽고 효율적으로 운영할 수 있도록 지원합니다.
창고 운영을 혁신할 준비가 되셨나요? 지금 바로 문의하여 Skypod® 시스템에 대해 자세히 알아보세요.