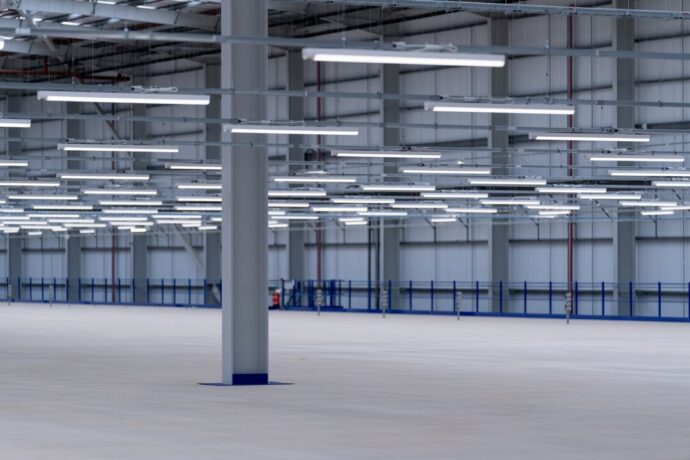
Site Visit and Analysis
We begin with a thorough site visit to understand your current operations and identify specific needs, ensuring our solution fits seamlessly into your space.
Streamline deployment for a smooth, predictable transition. Our expert-led approach, from system studies to go-live, minimizes disruption, maximizes performance, and gets your operations up and running faster than ever.
Our System Studies phase lays the groundwork for a successful deployment, preparing your site for automation. This vital stage involves:
We begin with a thorough site visit to understand your current operations and identify specific needs, ensuring our solution fits seamlessly into your space.
Our team performs risk assessments, rack calculations, and power dimensioning to anticipate challenges and plan efficient power use.
We produce detailed installation drawings and bill of materials to ensure all components fit perfectly within your existing infrastructure.
We use simulation tools to model system operations, including DeepSky® configuration and sprinkler impacts, to address issues early.
Our procurement team sources all essential Skypod® system components, focusing on high-quality materials for a robust automation infrastructure, ensuring durability and performance standards.
Our procurement team sources all essential components of your Skypod system. This phase focuses on gathering high-quality materials necessary for building a robust automation infrastructure, ensuring every part meets our stringent standards for performance.
Our software engineers collaborate with your IT team to integrate our software with your Warehouse Management System (WMS). This step ensures that the transition to automation is smooth, maintaining continuity without disrupting your existing workflows.
To further accelerate deployment, most equipment, including our conveyor systems, arrives pre-programmed. This approach eliminates common delays associated with traditional PLC programming, enabling faster setup and a quicker path to go-live.
The installation and commissioning phase is crucial for activating your warehouse automation system. Our approach ensures efficiency and precision.
After physical installation, we integrate the hardware with Deepsky and your Warehouse Management System (WMS). This ensures seamless communication between all components, setting the stage for optimal system performance.
Before going live, we conduct extensive safety and functionality tests on all robots and system interfaces. This rigorous testing guarantees peak efficiency, safe operation, and overall system reliability.
Beyond installation, we monitor performance, make adjustments, and gradually ramp up operations to meet initial objectives, ensuring the system reaches and maintains promised performance levels without disrupting operations.
The Provisional Acceptance stage ensures your automation system meets our performance and reliability standards. By the end, your system is fully installed, integrated, and ready for your team to use.
At this stage, we thoroughly test the system under real operational conditions, simulating day-to-day activities to ensure seamless performance and task handling.
Our team works diligently to validate that every component and system interface achieves 100% of of its nominal performance. This ensures that the system not only functions but excels.
Recognizing a system is only as good as its operators, we offer comprehensive staff training, typically under 30 minutes, to ensure all users are proficient with the new technology.
During this phase, we actively seek feedback from your team to make any necessary adjustments. This collaborative approach ensures that the system is fine-tuned to your operational needs.
Final Acceptance marks the culmination of our deployment, realizing our commitment to excellence and customer satisfaction. You gain an elegant automation system and a reliable partner dedicated to your success.
Our team ensures that the system consistently meets or exceeds the contractually guaranteed performance metrics. This stage is crucial for demonstrating the reliability and efficiency of the automation solution in actual working conditions.
Once the system meets performance standards, we hand over operational controls to your team, supported by comprehensive documentation and final training to ensure your staff is fully equipped to manage the system.
Our maintenance team is always on standby to provide ongoing support and ensure the system operates flawlessly all year round. We also offer 24/7/365 remote monitoring through our Control Center, capable of resolving 90% of system issues remotely.
We view the final acceptance not just as a project completion but as the beginning of a long-term partnership. We continually seek ways to optimize and enhance system performance to support your evolving business needs.
Exotec ensures the reliability of its automation systems through rigorous testing and quality assurance processes during and after installation. Our systems are designed with redundancy and fail-safes to minimize downtime. Additionally, we provide comprehensive training and 24/7/365 remote monitoring to ensure that our systems operate reliably around the clock.
Absolutely. Exotec’s warehouse automation solutions are tailored to fit various operational sizes, product types, and industry-specific requirements. Customization options include scalable robotics, software integrations, and adjustable system layouts to ensure compatibility with your existing processes.
To achieve optimal performance, the client must take specific standard actions before installing the Skypod system. These include floor planning and preparing storage areas. Anticipating these common preparations can help limit their impact on the installation schedule. Our sales engineers will guide you through all necessary preparations to ensure a smooth and efficient installation process.
Yes, a Skypod system can be installed in a warehouse without impacting ongoing production. The installation does not generate dust or heavy noise, allowing nearby activities to continue uninterrupted. Extensions to the existing Skypod system can also be implemented with minimal disruption, ensuring low negative impacts and limited production stops.
A dedicated Exotec team will manage your project from the contract signature until the system reaches the desired performance levels. Once production runs smoothly, our maintenance team will become your primary contact, providing ongoing maintenance support for at least 10 years to ensure the system continues operating at peak efficiency. Exotec’s extensive post-installation support includes preventive maintenance, system upgrades, and troubleshooting through our 24/7/365 control center. Additionally, we offer ongoing training for new staff and system updates to adapt to changing business needs or technological advancements.
Reach out to explore tailored automation solutions or get answers to your questions. Our team is dedicated to supporting your journey towards enhanced efficiency and success.