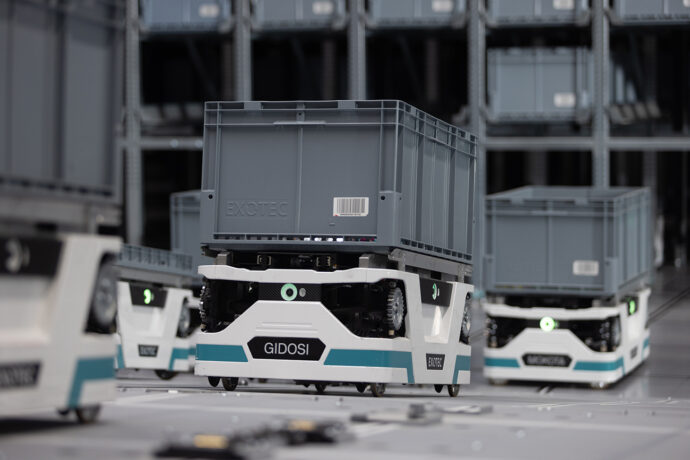

Automated Conveyor Systems for Your Warehouse
Skypath® is a plug-and-play automated conveyor system featuring straight, curved, and inclined building blocks along with a wide range of modules to meet diverse warehouse needs. Its modular design and pre-wired components ensure smooth integration and easy assembly within weeks.
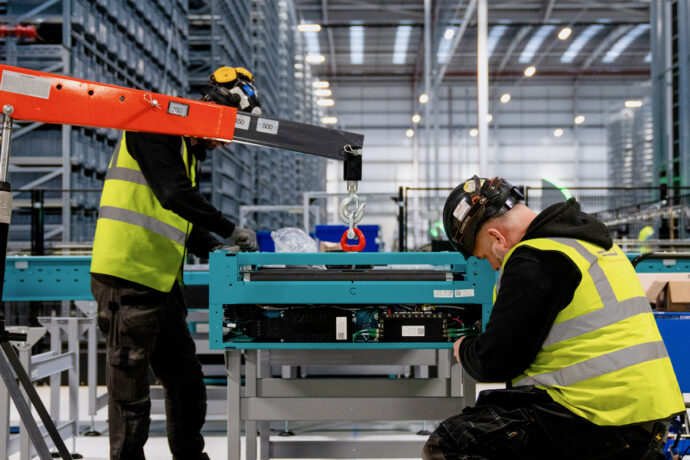
Quick Installation
Skypath® conveyor arrives pre-wired, eliminating the need for on-site PLC programming. The embedded software automatically identifies the conveyor layout, enabling the installation of 500 meters (1,640 feet) of conveyors in under 200 hours, making it a highly efficient automated conveyor system.
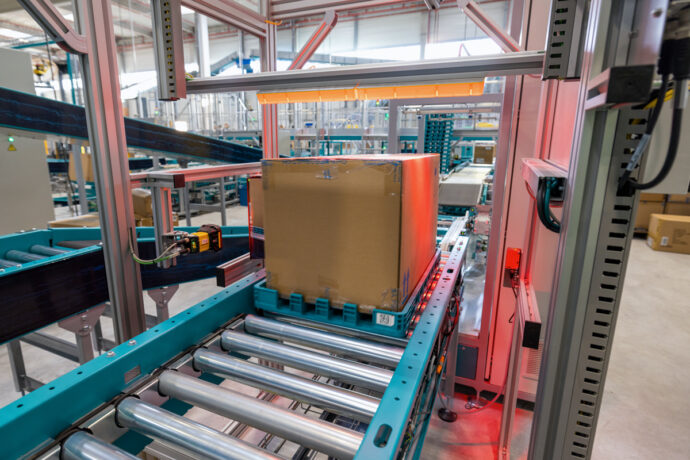
Unmatched Performance
Driven by the Warehouse Control System (WCS), Skypath® conveyor achieves a throughput of up to 2,600 totes per hour and speeds of 72 meters per minute (236 feet per minute). Built-in sensors and 24/7/365 support ensure rapid diagnostics and remote intervention, minimizing downtime.
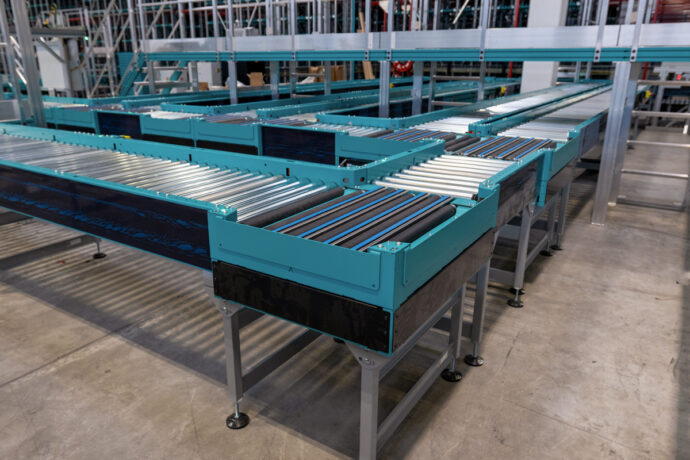
Adapts to Your Needs
With its modular design, including straight, curved, and inclined sections, as well as roller conveyors, belt conveyors, loaders, curves, transfer tables, and high-performance diverts, Skypath adapts to diverse logistics and warehouse layouts. The system is easily reconfigurable, meeting the demands of rapidly changing customer needs.
Technical Specifications
Characteristic | Specification |
---|---|
Section Types | Straights, 45° Curves, Transfer Tables |
Coating Type | Steel or PVC coated roller, Belt Over Roller |
Conveyor Widths | 512mm or 712 mm (20.2 to 28 in) |
Conveyor Lengths | 180mm to 2700mm (7.1 to 106.3 in) – for 512mm wide – Adjustable to the nearest mm 180mm to 2025mm (7.1 to 79.7 in) – for 712mm wide – Adjustable to the nearest mm |
Conveyor Heights | Up to 3 Conveying Levels – Max Height of 4500 mm (177.2 in) |
Standards Accessories | Barcode Readers, Safety Status Light, Emergency Stops, Reset Button |
Speed | Up to 72 m/min (236.2 fpm) |
Capacity | Up to 2,600 totes/hour (Straight & Curves – PVC/Steel) Up to 1,400 totes/hour (Belts and 90° Transfer Tables) |
Slopes | Up to 12° |
Industry Insights
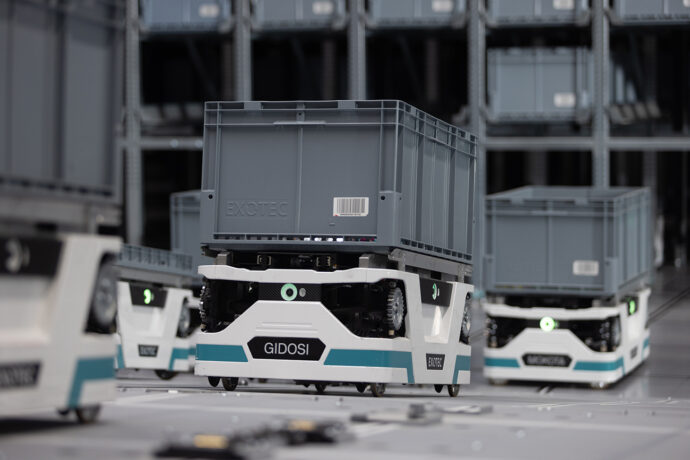
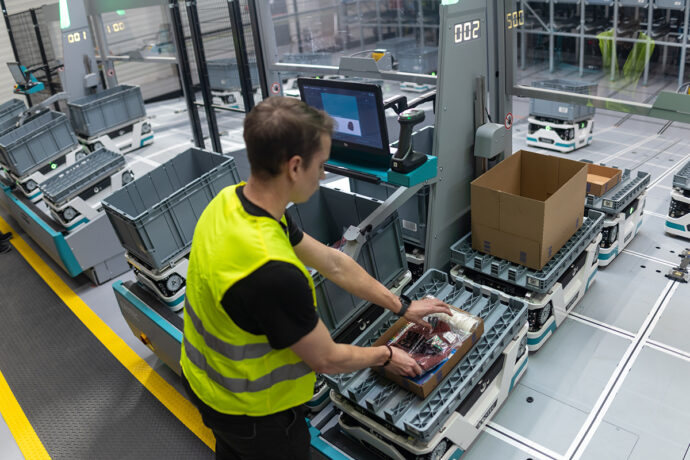
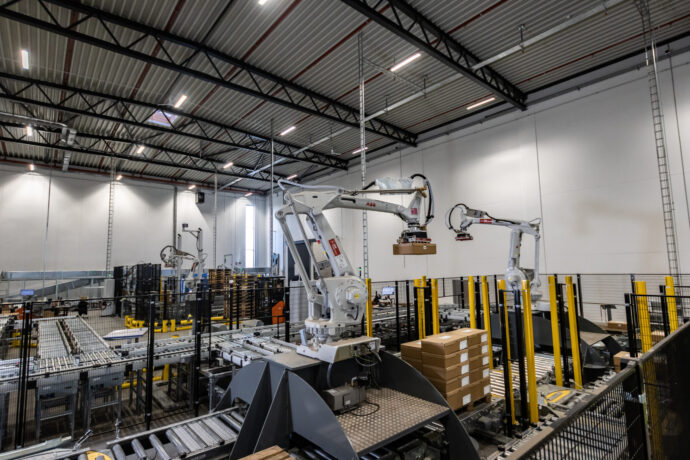
Frequently Asked Questions
Can Skypath® conveyor be purchased independently from the Skypod® system?
No, Skypath® conveyor is an integral component of the Skypod® system and cannot be purchased independently.
Does Skypath integrate with automation beyond the Skypod system?
Absolutely, Skypath is not just limited to integration with the Skypod system. It is a highly flexible solution engineered to work with various warehouse automation technologies. A key feature of Skypath is its capacity for automatic integrations with most API-based warehouse management systems. This capability ensures that Skypath can seamlessly connect with various existing systems, enhancing its utility and effectiveness in diverse operational environments.
What are the benefits and differentiating features of Skypath® conveyor compared to other automated conveyor systems?
Skypath® conveyor offers several key advantages over traditional automated conveyor systems: Ease of Installation: The pre-wired system simplifies the installation process. This feature eliminates the need for complex on-site PLC programming, reducing setup time and technical hurdles. Flexibility: Skypath’s modular design expedites installation and ensures that the system can be easily scaled up or modified as needed, making it ideal for evolving warehouse environments. Seamless Integration: Specifically engineered to integrate with the Skypod® system and other warehouse automation technologies, Skypath® conveyor enhances overall efficiency and coordination within the warehouse.
What is the installation process for Skypath® conveyor?
The Skypath® conveyor installation process is designed to be efficient, minimally disruptive, and expedient, with several key aspects ensuring a smooth implementation: Minimal Hardware Installation: The process is designed to minimize hardware installation requirements, thereby preventing significant disruption to ongoing operations at the site. This approach allows for a quicker setup and integration into existing warehouse activities. Embedded Software Assistance: Skypath® conveyor has embedded software that plays a crucial role in identifying the optimal conveyor layout. This technology dramatically speeds up the installation process by providing precise guidance on setup and configuration tailored to the specific needs of the warehouse environment. Modular Design: The inherent modular design of Skypath® conveyor further facilitates a faster and more adaptable installation. This design allows for quick adaptation to the evolving needs of warehouse operations and enables easier scaling in the future. Together, these factors ensure that the installation of Skypath® conveyor is a streamlined process, aligning with the operational tempo of modern warehouses and reducing downtime.
What considerations should I consider when integrating conveyor systems into my warehouse environment?
When integrating automated conveyor systems like Skypath® into your warehouse, it’s essential to consider the following: Operational Needs: Assess the volume, types of goods, and throughput requirements to ensure the conveyor system can meet these demands. Space Constraints: Evaluate your warehouse’s available space and layout to determine how the conveyor system can be optimally configured. Integration with Existing Systems: Ensure that the conveyor system seamlessly integrates with warehouse management systems and other automation technologies like the Skypod® system. Budget: Determine your budgetary constraints considering the upfront investment and the long-term operational savings.
Scalability: Assess the scalability of the conveyor system to ensure it can grow alongside your evolving operational needs.
Maintenance and Support: Consider the maintenance level required and the vendor’s support.
Connect with Us
Ready to enhance your warehouse operations? Contact us to learn how Skypath modules can be seamlessly integrated with your Skypod® system, bringing more value and peace of mind to your warehouse operations.