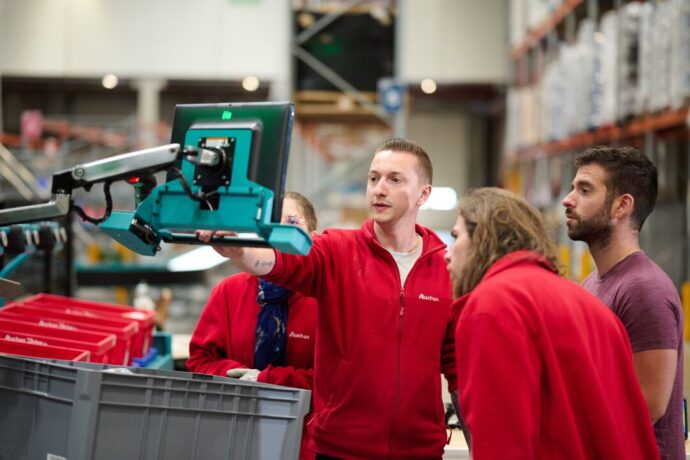
Auchan Luxembourg transforms drive and e-commerce order preparation
Our retail experience at the service of a European leader
With the installation of the very first Next Generation Skypod® system, the E.Leclerc Seclin Drive-through grocery store has substantially optimised order preparation and storage to offer its customers a smoother, faster and more service-oriented Drive-through experience. This project marks a significant step forward in the growth of this company, but also in the history of Exotec®.
Faced with rapid growth in its customer base, the E.Leclerc Seclin Drive-through grocery store was facing some major challenges:
At the outset of the project, E.Leclerc Seclin was looking for a logistics solution capable of meeting its various challenges. Maxence Maurice, director of E.Leclerc Seclin, had been closely following the robotic innovations proposed by Exotec, and the decision to opt for the Skypod system was a natural one. ‘I chose Exotec systems for their storage density and operational flexibility,’ he explains. Combining the company manager’s strategic vision with Exotec’s continuous innovation process, this collaboration provided an ideal testing ground, which ultimately gave rise to a whole new generation of Skypod products.
Robots | Storage bins | System height | System footprint | Drive-through stations | Clients served |
30 | 1,680 | 6 m (20 ft) | 2,500 m² (26,910 ft2) | 12 | Up to 110 customers per hour and 1,200 customers per day |
The process begins with the manual collection of items by operators. Operators proceed in successive waves, collecting products in the same category for several customers at the same time, in order to optimise picking time.
The collection bins are transported to sorting tables by Skypath® conveyors, where they are sorted. The items are placed in customer bins, each corresponding to a customer order.
Once the bins have been assembled, they are directed to three specific zones, determined by the storage temperature of the items they contain:
As soon as customers arrive at the Drive-through pickup, they sign in via an external terminal, which simultaneously triggers the extraction of bins from the three storage areas (ambient, fresh and frozen). Synchronised conveyors group the bins in buffer loops located above the 12 automated delivery stations, specially designed for this project and featuring an innovative design.
When the customer pulls up to a station, the bins are automatically lowered in a continuous flow, ready to be stowed directly in the boot.
As well as guaranteeing smooth, fast delivery with no unnecessary waiting, the automation of the Drive-through supermarket gives operators the opportunity to concentrate on customer reception and service. With a permanent presence in the Drive-through car park, operators can intervene if necessary, without being tied down by the constant flow of orders to customers.
‘Today, we’ve been able to expand our business, meet consumer demand and prepare more orders.’
The installation of the new generation Skypod system has enabled E.Leclerc Seclin to achieve impressive results:
Thanks to this collaboration between E.Leclerc Seclin and Exotec, Drive-through grocery is now positioned as a model of efficiency and innovation. This project proves that an advanced logistics system, such as the Next Generation Skypod system, can transform the customer experience while optimising operational performance and employee well-being.
Our retail experience at the service of a European leader
Flexible Ambient Fresh Grocery Order Fulfillment
Efficiently Navigate Growth Sales Peaks