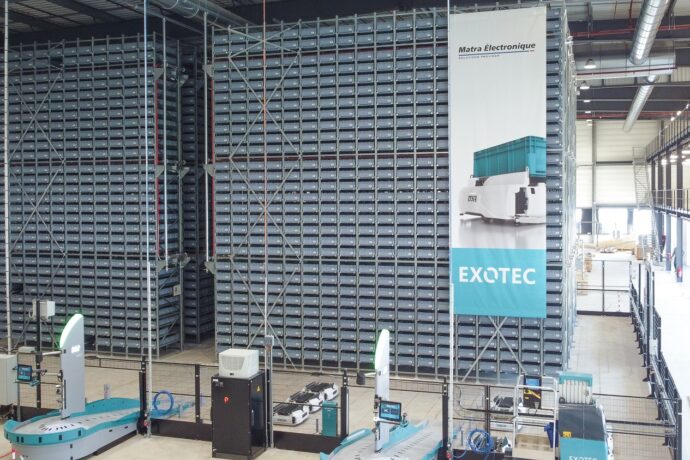
Industry
Share
In partnership with Exotec® and the installation of the Skypod® system in the Dudelange warehouse, Auchan Luxembourg has transformed its e-commerce order preparation and distribution processes. This has enabled it to achieve high levels of performance and quality for its customers, and to support its ambitions in terms of development.
About Auchan Luxembourg
Since the opening of its first store in 1996, Auchan Luxembourg has grown to include 7 stores, including 3 hypermarkets. With an e-commerce branch offering drive-through and home deliveries, the company is constantly innovating to enhance the quality and responsiveness of its warehousing and preparation, for the benefit of its customers. Faced with the rapid expansion of e-commerce activities and the desire to open new distribution outlets, Auchan Luxembourg is positioning itself as a major, forward-thinking player in the mass retail sector.
The challenge
Since 2006, Auchan Luxembourg has relied on a “master” warehouse in Dudelange, in the south of the country, to prepare and distribute its e-commerce drive-through and home orders – the company also aims to develop in-company delivery. Stocked in 4 different temperature zones – dry, fresh, frozen and fruit & vegetables – products of all sizes are stored and prepared here, before being dispatched to the various order distribution points.
The project is part of a constrained and changing context. It is the final building block in a wide-ranging overhaul of Auchan Luxembourg’s e-commerce processes and tools: new website, new ERP, new WMS (MAGISTOR). At the end of the chain, in order to finalize this new logistics deal, a project to automate the Dudelange warehouse, to densify storage, rationalize preparation and dispatch operations, and reduce drudgery for employees working on the installation.
After a period of consultation with various companies, Auchan Luxembourg turned to Exotec, attracted by the “all-inclusive” aspect (modularity of the system, integration of specific software and machines, maintenance included…) of our solution. “We benefited from a 100% turnkey service”, explains Martin Delattre, Logistics Operations Manager at Auchan Retail Luxembourg.
What else convinced the retailer? Exotec’s proven experience with other major retail companies, and its ability to understand the business issues at stake in pre-sales, deployment and maintenance, and to provide solutions to the specific problems encountered by Auchan Luxembourg, by speaking a common language. “Right from the pre-sales phase, we were dealing with people who not only had a perfect grasp of the system, but also of our problems, having encountered them at other customers in the sector […] This made the workshops very productive”, adds Martin Delattre.
The first Exotec site in Luxembourg, and a successful first collaboration! See below for full details of this exemplary project.
“Exotec’s turnkey system, coupled with a keen understanding of our specific needs, simplified our transition to automation.”
The Solution
- Number of robots: 37
- Number of picking stations: 3
- Number of bins: 2x 15,300
- Number of bins per hour: 915
- Floor area of system: 749 m².
1. Performance improvement
- Capacity to handle up to 915 bins per hour, optimizing order picking times.
- Centralize picking and restocking operations, reducing inventory errors and improving stock accuracy.
- Flexibility of stations, allowing preparation and reception to be carried out on the same workstations, increasing operator versatility.
2. Reducing drudgery
- Automation eliminates repetitive manual tasks and physical constraints.
- Improved working conditions: pickers no longer have to handle heavy products or work in uncomfortable positions.
- Reduced internal travel for preparation staff, increasing efficiency and reducing fatigue.
3. Turnkey solution
- Complete integration of system, machines and software, ensuring uninterrupted operational continuity.
- Maintenance included, with options such as system cleaning, allowing Auchan to concentrate on its core business.
- Team support and training by Exotec, facilitating rapid adoption of the new system.
4. Storage densification
- Optimization of available space, enabling an increase in the number of references stored.
- A flexible, scalable system, designed to absorb future stock increases and manage seasonal or promotional variations.
- Use of specific Auchan bins for preparation and delivery, maximizing logistical efficiency.
5. Efficient returns management
- Simplified management of customer returns with a multi-reference storage system.
- Automatic prioritization of returned items for rapid reintegration into active stock.
- Reduce inventory errors and optimize receiving productivity.
Related Case Studies
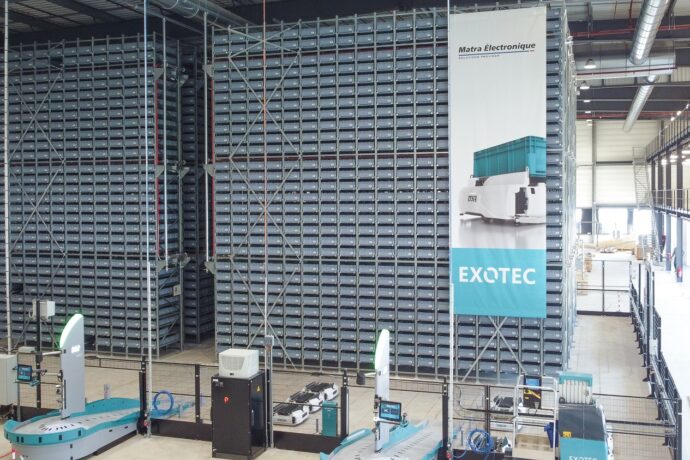
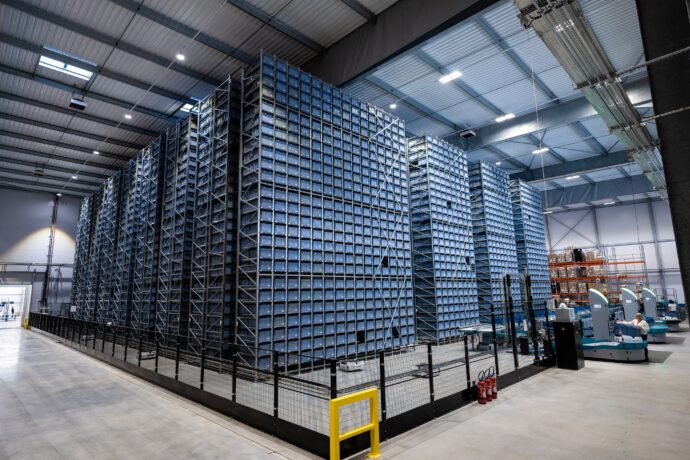
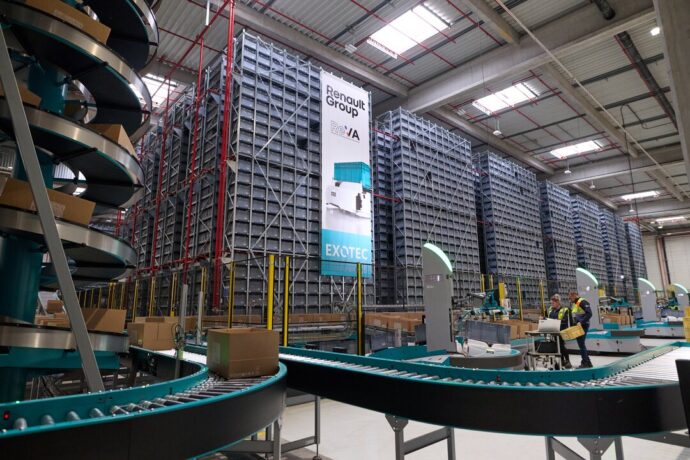
Renault Group: Streamlining Spare Parts with Warehouse Automation
Efficient Intralogistics for Automotive Spare Parts
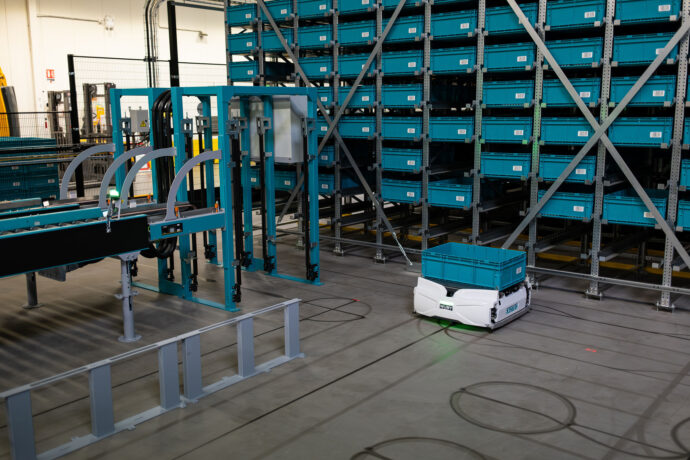
bioMérieux: supporting growth through robotisation in a regulated healthcare sector
When health and robotic automation go hand in hand