Industry
Share
About LACROIX
LACROIX Group is an international technology equipment supplier, providing smart, connected and secure equipment and solutions to improve the management of road, water and energy infrastructures. Its Electronics business, with which we had the honour of working, is even ranked in the top 50 Electronics Manufacturing Services (EMS) worldwide. Its services range from the design to the manufacture of electronic equipment for markets such as automotive, industry, connected homes & buildings, aerospace & defence and healthcare.
The challenge
Move and optimise. Previously located in an old industrial building in Maine-et-Loire, LACROIX’s Electronics business decided in 2022 to move its operations to a brand new building, designed with a threefold approach of industrial, social and environmental innovation in mind.
The main aim of the move – and this is where Exotec comes in – was to increase the reliability and performance of the storage and preparation of electronic parts and other plastic and metal parts (over 4,000 references). These will then be used in the production of embedded systems and other connected objects for LACROIX customers. The ‘store’, where these parts are stocked, is therefore at the heart of the company’s business. Without optimal operation of the warehouse in terms of throughput, but also in terms of precise knowledge of the items in stock, the entire preparation chain can be affected.
In the context of the move, the aim was also to enable the business to restart very quickly. “We could only stop our equipment for a week,” explains Claude Bourget, manager of the Beaupréau site and of LACROIX’s Electronics business. And when it came to restarting, the promise was indeed there: “It worked from day one, it was plug & play, and we hardly had any fine-tuning phase“.
Increased human value. Previously largely manual, these storage and preparation operations involved walking and carrying loads for operators. This meant a loss of added value for the company, which had to assign its employees to these often repetitive tasks. Thanks to the Skypod intralogistics automation system, these operators can now take on tasks that are more rewarding for the company and more rewarding for the employees, a point that is also very important for the Anjou-based manufacturer: “We’ve virtually eliminated non-value-added operations in the warehouse, which has enabled us to reposition our teams on more interesting tasks”, says a delighted Claude Bourget. And so are his staff, we imagine…
The solution
Results
1. Increased performance
- 7-fold increase in productivity
2. Improved efficiency
- Reduced travel and non-value-added tasks for operators
3. Optimised ergonomics
- Ergonomic stations to facilitate picking, intuitive handling of the system
4. Space saving
- Double-depth rack storage, making the system 20% denser than conventional systems, saving 500-600 m² of warehouse space.
5. Fast, reliable commissioning
- The system was installed in less than 15 months, with storage and parts preparation activities restarting immediately after the move, with complete reliability.
6. Industry 4.0 made in France
- A successful collaboration between two of France’s industrial flagships, helping to relocate innovative activities as close as possible to local areas.
Related Case Studies
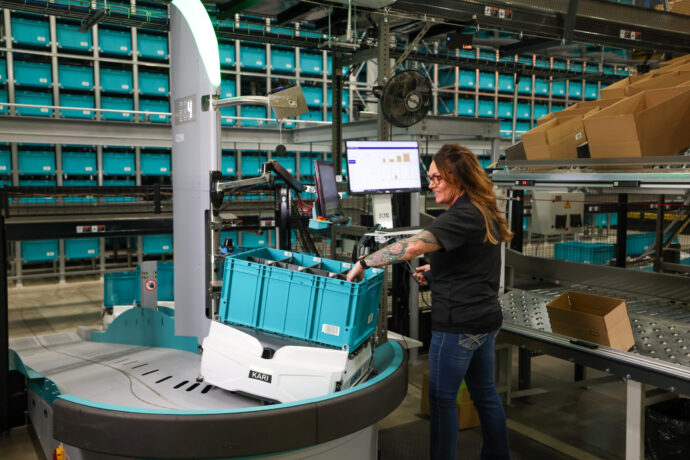
Lane Automotive: Boosting Efficiency with Warehouse Automation
Delivering Seamless End-to-End Order Fulfillment
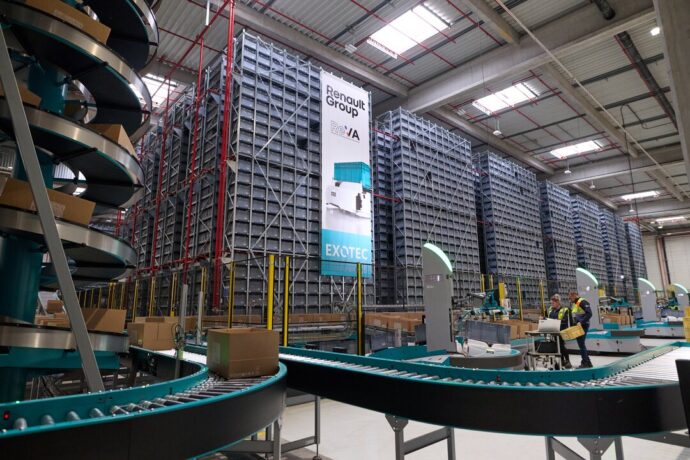
Renault Group: Streamlining Spare Parts with Warehouse Automation
Efficient Intralogistics for Automotive Spare Parts