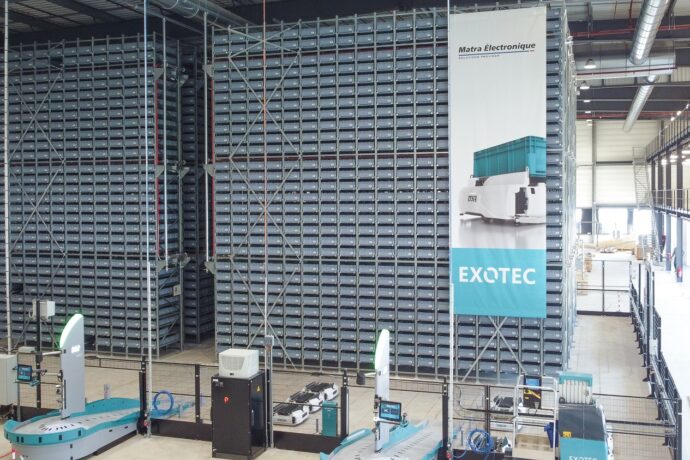
Industry
Share
In a post-COVID world where public health challenges are numerous and complex, global in vitro diagnostics specialist bioMérieux is seeing its sales grow every year. To continue to serve its customers rapidly and anticipate future growth while respecting its social and environmental commitments, the company has decided to opt for the robotisation of part of its logistics facilities. Close-up of the Saint-Vulbas International Distribution Center (France), where the Skypod warehouse automation solution finds its first application in the healthcare sector.
About bioMérieux
Improving public health worldwide
Founded in 1963, bioMérieux develops, manufactures and markets in vitro diagnostic solutions (systems, reagents, software and services) in two fields of application:
- Clinical applications (85% of business): providing hospitals and laboratories with solutions to determine the origin of diseases – mainly infectious diseases – and thus improve patient health.
- Industrial applications (15% of business): providing manufacturers with solutions to detect the presence of micro-organisms throughout the production chain and guarantee the quality of food and pharmaceutical products to ensure consumer safety.
With its three flagship technologies (microbiology, immunoassays and molecular biology), bioMérieux is one of the world leaders in in vitro diagnostics. With over 90% of its sales generated outside France, bioMérieux is present in 45 countries and markets its products in more than 160 countries through a large network of distributors.
Pyramid supply chain
From production to the end customer, the French company’s logistics organisation is based around two International Distribution Centres (located in France and the United States respectively), which receive and store all manufactured products. Depending on the context, these distributors then supply either bioMérieux’s distribution subsidiaries in 45 countries, or partner distributors in other countries around the world.
It should be noted that bioMérieux’s two international distribution centres also handle order preparation and distribution in the regions where they operate. bioMérieux’s International Distribution Centre in Saint-Vulbas (Ain) not only supplies the company’s subsidiaries and partner distributors around the world, but also its end customers in France, Italy, Spain, Switzerland and Ireland.
The challenge
Against the backdrop of the world’s growing need for diagnostic solutions, bioMérieux posted organic sales growth of 10% in the first half of 2024, confirming the company’s constant and steady growth, its strength in innovation and its ability to adapt to the needs of the sector.
An ambitious project, and the first Skypod system in the healthcare sector
To anticipate this growth, and ensure that its order-picking performance is maintained at all times, the company is also focusing on modernising its intralogistics equipment. 20 years after its commissioning in 1999, the Saint-Vulbas International Distribution Center underwent a complete overhaul, in which intralogistics robotics company Exotec® participated by supplying bioMérieux with the very first Skypod system for the healthcare sector.
Right from the start of the project to modernise the Saint-Vulbas site, ambitions were set to make it an exemplary facility, with a number of challenges to be met along the way:
- Supporting the company’s growth – with the ultimate aim of shipping 5,000 parcels and 400 pallets a day
- Increase in storage capacity – currently 15,000m2
- Choosing equipment that promotes safety and well-being in the workplace.
- Reduction of the project’s carbon footprint, through a much more energy-efficient building and a reduction in the volume shipped thanks to a mix of temperatures in the packages and the integration of a Jivaro machine.
- Control of storage and transport temperatures – crucial in the health sector – from the distribution centre to the end customer’s supply chain
- Complete replacement of the information system with a view to modernisation
- Insertion of an automated order-picking system – in this case, a Skypod system
Integration into existing installations and constraints
In the warehouse, 3 sizes of cardboard boxes are first formed for order picking, then routed either to a picking area with stations for products stored between 2 and 8°C, or to the Skypod system in which products are stored at a temperature of 15 to 25°C. Once they have passed through one of the two preparation areas, the complete parcels are then directed to the end of the line, where a special Jivaro (Savoye) machine adjusts the height of the cartons according to their contents, and where they are sealed.
In a pre-existing space, and a building constrained in terms of available volume, the Skypod system had to elbow its way into place, and integrate with bioMérieux’s intralogistics operations: “The station preparation area is immovable, as is the end of line for packaging and labelling, so it was essential for the Skypod system to fit into the limited space available, and to be able to share the parcel preparation area between the existing system and the Skypod system”, explains Frank Reverdy, IDC 2040 Project Director at bioMérieux. This sharing of resources between two very different types of preparation facility not only saves space, but also offers the prospect of future environmental gains: ‘Eventually, and with the agreement of our customers, we plan to prepare packages containing both 2-8°C and 15-25°C products. Combined with the reduction in carton height, this process will enable us to save around 15% in parcel volume, according to our estimates,‘adds Frank Reverdy.
The solution
1. Improving productivity
- Efficience des robots AMR Skypod : fonctionnement 24/7
- High level of ergonomics for the operator
- Skypod autonomous robots move at a speed of 4 metres per second
- Integration of an Exotec exit conveyor and a measuring conveyor for weighing parcels
- 98% guaranteed performance
2. Flexibility and integration in a constrained environment
- Skypod system sized to meet requirements at time T
- Automated system that integrates into the existing intralogistics workflow
- Integration of specific traceability and quality constraints specific to the healthcare sector
3. Intralogistics and environmental efficiency
- Range of products stored between 15 and 25°C reinternalised and automated thanks to the Skypod system
- Pooling of different preparation methods to improve the site’s logistical and environmental efficiency
- Energy consumption and sustainability in line with bioMérieux objectives
4. Well-being at work
- Optimum height of preparation stations
- Postures and conditions for handling items in line with ergonomic best practice, validated by an ergonomist appointed by bioMérieux
- Operators appreciate the simplicity and intuitiveness of the system
The advantages of the Skypod intralogistics automation solution
The Skypod warehouse automation system offers numerous advantages and anticipates future challenges in the pharmaceutical industry.
● Increase throughput and treatment capacity
● Anticipating future growth by enabling scalability of intralogistics operations
● Offer scalability and modularity for the system
● Guarantee a 24/7/365 maintenance and support service for AMRs
‘The strength of the Skypod system is that it has allowed us to invest in the number of robots we need today, not the number of robots we will need tomorrow.’
Frank Reverdy, IDC 2040 Project Director at bioMérieux
Related Case Studies
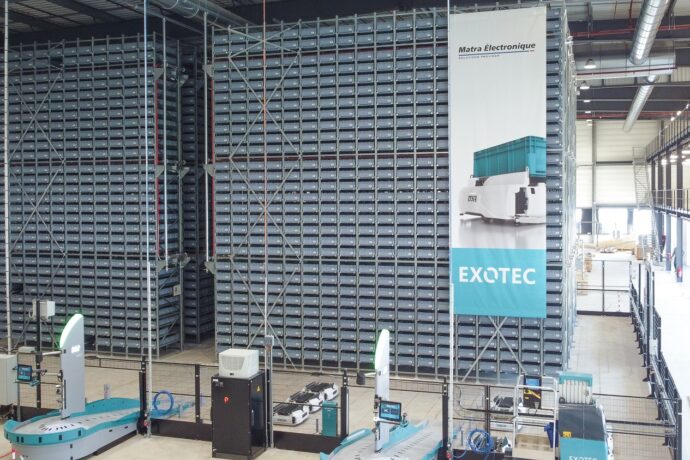
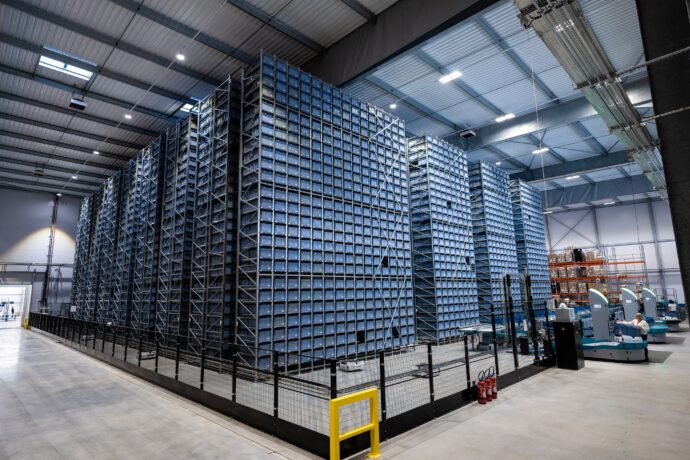
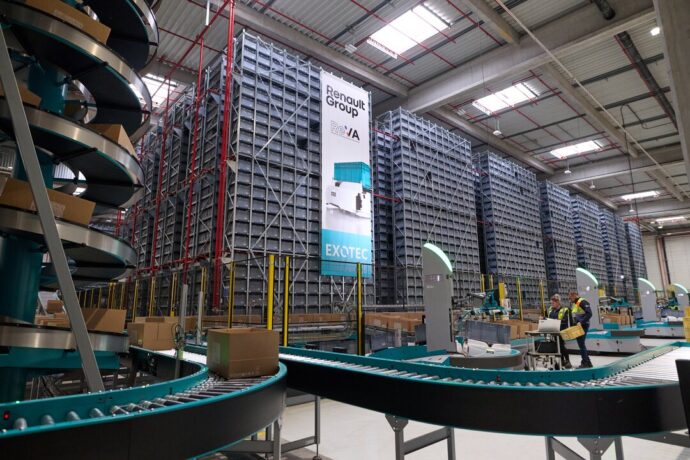
Renault Group: Streamlining Spare Parts with Warehouse Automation
Efficient Intralogistics for Automotive Spare Parts

Supplyweb: Enhancing 3PL Efficiency through Warehouse Automation
Turn your robotics tool into a selling point