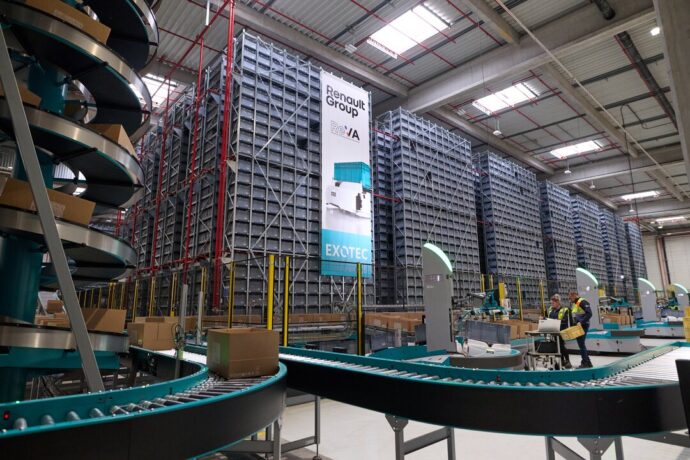
Industry
Share
In a post-COVID world where public health challenges are numerous and complex, global in vitro diagnostics-specialist, bioMérieux is seeing its sales grow every year. To continue serving its customers rapidly and anticipate future growth while respecting its social and environmental commitments, the company has decided to opt for the robotization of part of its logistics facilities. At the International Distribution Centre in Saint-Vulbas, France, the newly installed Exotec® Skypod® system stands at the center of bioMérieux’s warehouse logistics. Let’s delve into this innovative development.
About bioMérieux
Improving Public Health Worldwide
Founded in 1963, bioMérieux develops, manufactures, and markets in vitro diagnostic solutions (systems, reagents, software, and services) in two fields of application:
- Clinical applications (85% of business): providing hospitals and laboratories with solutions to determine the origin of diseases – mainly infectious diseases – and thus improve patient health.
- Industrial applications (15% of business): providing manufacturers with solutions to detect microorganisms throughout their production chain, ensuring the quality and safety of food and pharmaceutical products for consumers.
With its three flagship technologies (microbiology, immunoassays, and molecular biology), bioMérieux is one of the world leaders in in vitro diagnostics. With over 90% of its sales generated outside France, bioMérieux is present in 45 countries and markets its products in more than 160 countries through a large network of distributors.
Pyramid Supply Chain
From production to the end customer, the French company’s logistics organization is based around two International Distribution Centers (located in France and the United States), which receive and store all manufactured products. Depending on the context, these distributors then supply either bioMérieux’s distribution subsidiaries in 45 countries, or partner distributors in other countries around the world.
It should be noted that bioMérieux’s two international distribution centers also handle order preparation and distribution in the regions where they operate. bioMérieux’s International Distribution Centre in Saint-Vulbas not only supplies the company’s subsidiaries and partner distributors around the world, but also its end customers in France, Italy, Spain, Switzerland and Ireland.
The Challenge
Amid the world’s increasing demand for diagnostic solutions, bioMérieux reported a robust 10% organic sales growth in the first half of 2024. This performance highlights the company’s consistent and steady growth, its strength in innovation, and its agility in meeting industry needs.
An Ambitious Project and First Skypod System in the Healthcare Sector
To anticipate this growth and maintain top-notch order-picking performance, the company is modernizing its intralogistics equipment. Twenty years after its inauguration in 1999, the Saint-Vulbas International Distribution Centre has undergone a comprehensive overhaul. Exotec® played a key role in this transformation by providing bioMérieux with the first Skypod system for the healthcare sector.
From the project’s inception, the goal was to create an exemplary facility, tackling several challenges along the way:
- Support company growth with the goal of shipping 5,000 parcels and 400 pallets per day
- Increase storage density of 15,000 m2 warehouse
- Utilize equipment that promotes safety and well-being in the workplace
- Reduce the operational carbon footprint with a more energy-efficient building while minimizing shipping materials by incorporating mixed-temperature parcels and utilizing machines to reduce empty space per parcel
- Ensure precise control of storage and transport temperatures, critical in the health sector, from the distribution center to the end customer
- Replace outdated information system to modernize operations
- Implement an automated order-picking system, specifically a Skypod system
Integration Into Existing Installations and Constraints
In the warehouse, three sizes of cardboard boxes are formed for order picking. These boxes are then routed to either a picking area with stations for products stored between 2 and 8°C, or to the Skypod system, where products are stored at temperatures of 15 to 25°C. After passing through one of these preparation areas, the complete parcels are directed to the end of the line. Here, a special Jivaro (Savoye) machine adjusts the height of the cartons according to their contents and seals them.
In a pre-existing space with limited available volume, the Skypod system had to be carefully integrated with bioMérieux’s intralogistics operations. The station preparation area and the end-of-line packaging and labeling area are immovable, making it essential for the Skypod system to fit into the remaining space and share the parcel preparation area with the existing system.
Frank Reverdy, IDC 2040 Project Director at bioMérieux, explains, “This sharing of resources between two very different types of preparation facilities not only saves space but also offers the prospect of future environmental gains. Eventually, and with the agreement of our customers, we plan to prepare packages containing both 2-8°C and 15-25°C products. Combined with the reduction in carton height, this process will enable us to save around 15% in parcel volume, according to our estimates.”
The Skypod System Solution
Robots | Picking Stations | Replenishment Stations | Bins | Bins/Hour | Rack Height | System Footprint |
---|---|---|---|---|---|---|
12 | 2 | 1 | 8,000 | 300 | 9 m (29.5 ft) | 675 m2 (7,265 ft2) |
1. Improving Productivity
- Robots can retrieve any item within the system in just 2 minutes, ensuring tight order cutoff times are met
- 2 ergonomic picking stations capable of processing 250 bins per hour with just two employees, and a replenishment station that can handle 50 bins per hour with a single employee
- Enables 24/7 order fulfillment operations with 98% guaranteed performance
2. Enhancing Flexibility Within a Constrained Facility
- Seamlessly connected with inbound and outbound system including carton formers, closers and weight scales
- Complies with stringent healthcare standards, ensuring high-quality and precise tracking of individual items
3. Elevating Environmental Efficiency
- Automates and reinternalizes the storage of products maintained between 15 and 25°C
- Lightweight robots use relatively minimal energy, ensuring that energy consumption and sustainability are aligned with bioMérieux’s objectives
‘The strength of the Skypod system is that it has allowed us to invest in the number of robots we need today, not the number of robots we will need tomorrow.’
Frank Reverdy, IDC 2040 Project Director at bioMérieux
Related Case Studies
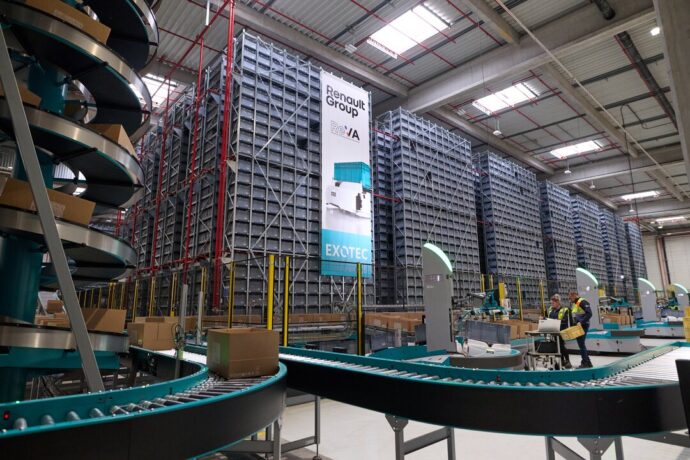

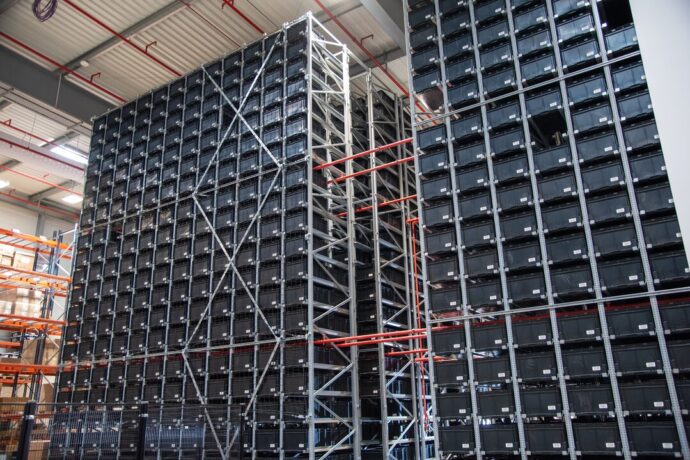
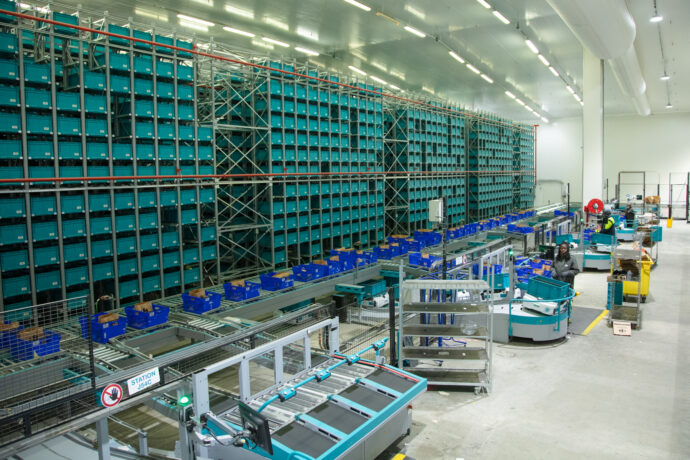
Carrefour Le Plessis-Paté, France – Case Study
Flexible Ambient & Fresh Grocery Order Fulfillment