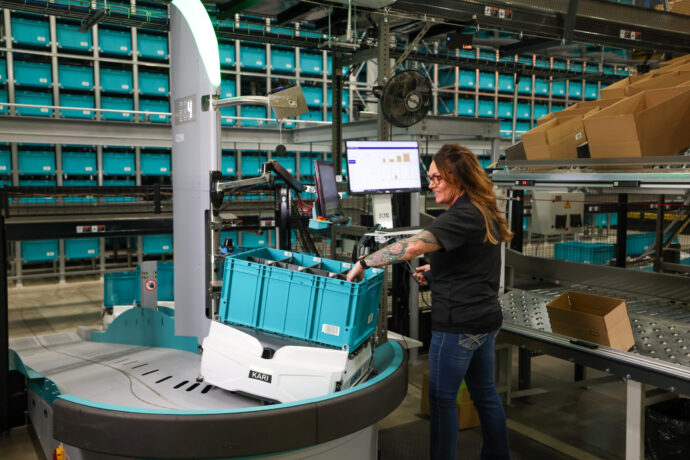
Industry
Share
Thanks to a strategic partnership with Exotec® and the integration of the Skypod® system in its Villeroy warehouse, Renault Group is strengthening its spare parts and accessories supply chain, guaranteeing high standards of performance and quality for its customers.
About Renault Group
Renault Group, a global leader in the automotive industry, sets itself apart with its unwavering commitment to innovation and process optimization, especially in logistics. This commitment is exemplified by the streamlined management of its spare parts supply chain, overseen by the company’s Parts and Accessories Logistics Department (DLPA).
The Challenge
Renault Group faced a number of major challenges in managing its after-sales parts logistics in Europe:
- Fragmentation of the distribution system: with warehouses specialized by part family rather than by geographical market, leading to inefficiencies
- Lack of a regional distribution warehouse for France: limiting capacity to meet national demand, which accounts for 37% of DLPA’s business
- Need for Innovation: Dependence on outdated equipment and systems undermining the quality of customer service
In response to these challenges, Renault Group initiated the OTAGO project to revamp the master plan for its warehouses in France. The project focuses on centralizing distribution operations and tailoring warehouses to specific markets. Upon the project’s conclusion, it was determined to fully reorganize the warehouses dedicated to spare parts:
- Closure of the Cergy warehouse: Replaced by a new site in Puiseux, dedicated to serving European and international markets
- Transformation and modernization of the Villeroy warehouse: Designated as the primary distribution center for France
- Specialization of the Flins-sur-Seine warehouse: Focused on storing and distributing heavy and bulky parts for both French and global markets
The Skypod System Solution
Robots | Picking Stations | Replenishment Stations | Storage Bins | Bins/Hour | Rack Height | System Footprint |
191 | 14 | 2 | 66,700 | 4,000 | 10.8 m (33 ft) | 5,590 m2 (60,170 ft2) |
Key Results
1. Optimizing Customer Service
- Ability to dispatch all parts ordered up to 5:30 PM for next-day delivery by 8:00 AM, ensuring swift and timely fulfillment
- Consolidation of over 80% of French business into a single warehouse, significantly reducing order processing times and streamlining logistics
- Achieved a customer service satisfaction rate exceeding 99.7%, demonstrating a high standard of reliability and commitment
- Integrated over 15,000 product references, with a long-term target of 20,000, ensuring a broad and diverse selection of available parts
2. Reducing Costs and Improving Productivity
- Improved productivity within the ReVA perimeter by a factor of 4, aiming to handle 20,000 order lines per day, dramatically cutting customer order processing times
- Skypod system capable of processing up to 4,000 lines per hour during peak periods
- Reduced order processing time from 120 minutes to just 15 minutes, significantly enhancing efficiency and customer satisfaction
- Stabilized and reduced reliance on temporary staff, resulting in a more consistent and reliable workforce
3. Sustainability and Innovation
- Utilized 67,000 recycled plastic bins, highlighting Renault Group and Exotec’s commitment to sustainability
4. End-to-End Integration of Specialized Machines
- Exotec integrated a range of specialized machines in tandem with the Skypod system, including two carton forming machines, two closing machines, three packing list printers, two RFID shipping label printers, a wrapping machine, and 30 ergonomic grippers, to enhance operational efficiency and automation
- Integration of Dealer Label printers at picking stations to improve inventory traceability and stock management
- Incorporated a trashline system directly into the injection stations, optimizing waste management processes and maintaining a clean and orderly workspace
“Keeping to the schedule and achieving our ramp-up curve were major challenges. We are satisfied with the results achieved so far and are preparing to finalise the organisational transformation around this new facility.”
Louis Szukics, Warehouse Engineering Manager – Transformation Division at Renault Group
Related Case Studies
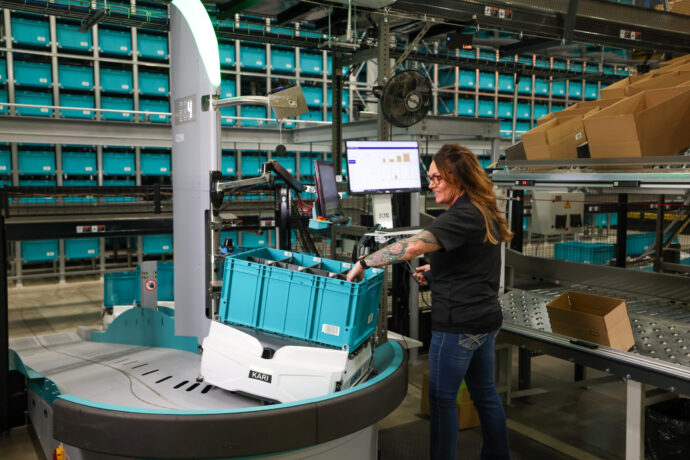
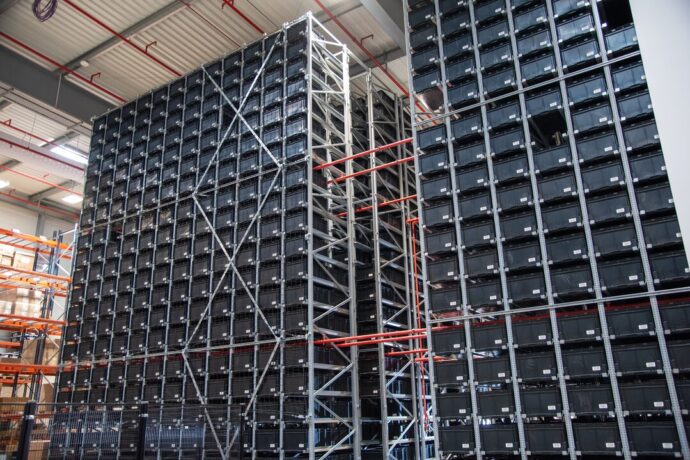
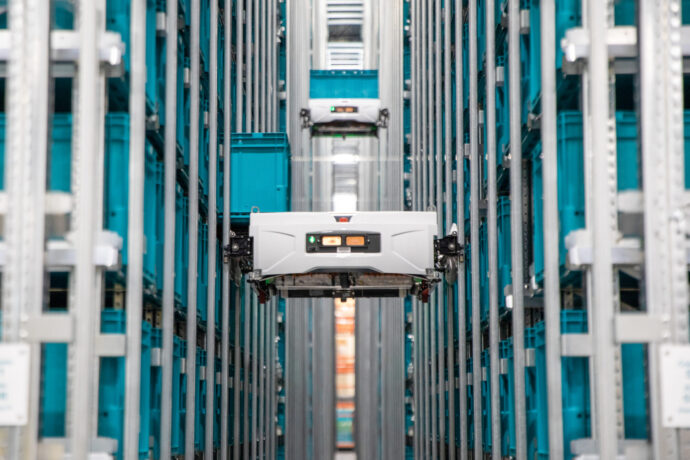